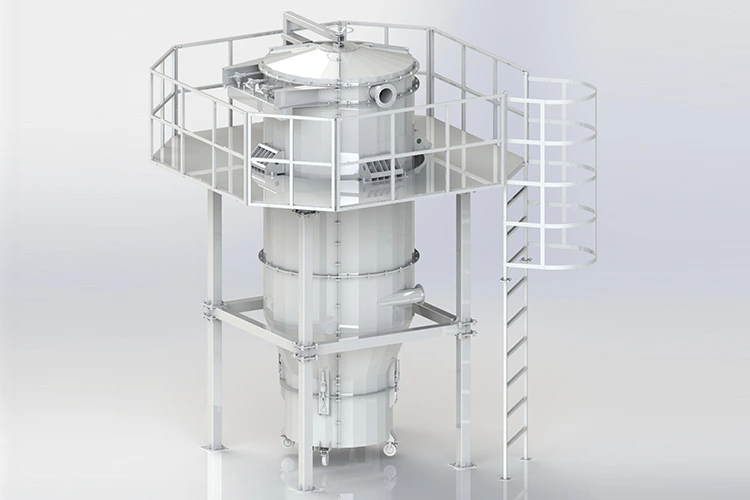
Explosion-proof industrial vacuum cleaner
Industrial explosion-proof (Ex-proof) vacuum cleaner designed to work with sugar dust combined with the central cleaning system of the sugar mill.
Industry:
Services:
TRL:
1 → 9
Project duration:
3 months
Industrial explosion-proof (Ex-proof) vacuum cleaner designed to work with sugar dust combined with the central cleaning system of the sugar mill.
Industry:
Services:
TRL:
1 → 9
Project duration:
3 months
The client required a custom industrial vacuum cleaner that would ensure safe operation in an explosive dust zone (sugar dust). The sugar dust required a safe separation and accumulation.
The filter unit had to comply with and be retro-fitted in the plant’s pipeline network (in accordance with the design documentation for the reconstruction of the sugar mill). The vacuum cleaning process was centralized and the vacuum cleaning unit provides enough power to collect dust from remote areas of the plant.
The Ex-proof design was a must for this filter, to protect the staff and the mill’s equipment in the sugar mill’s hazardous environment.
Laser cutting CNC
Sheet metal bending CNC
Welding
Milling & lathe CNC
Antistatic Ex-proof coating
Pulse jet cleaning system
Custom programmable logic controller (PLC)
Centrifugal vacuum blower
Differential pressure sensors (Ex-proof)
Ex-proof wiring design (ATEX)
We started the project by developing the technical concept to ensure compliance with the plant’s engineering infrastructure. Sleeves filter elements were selected to collect the sugar dust. In order to choose the right amount of filter elements, a series of calculations were carried out. The number of filters, size, and filtration surface area depend on the amount of dust produced at the mill’s floor.
The filter calculations provided data for the conceptual CAD design of the vacuum cleaner. The concept of the cylindrical shape unit comprised three main modules:
The developed concept underwent a series of CFD simulations (computational fluid dynamics)to determine the optimal air/dust flow through the filter’s internal cavity.
In the CFD analysis, the parameters of the centrifugal separator were determined and fixed (e.g. dimensions of the funnels, the dimensions of the inlet channel, etc.). Simulations were needed to ensure the required separation and deposition of coarse dust particles in the dust collector.
Further, we analyzed and specified the requirements for the high-pressure blower. Therefore, an additional set of CFD simulations was carried out, feeding the available data of the aerodynamic resistance inside the inner cavity with installed bag filters. The simulations suggested the use of a powerful blower delivering ~30 kPa pressure.
Pulse regeneration jet cleaning (filter regeneration/cleansing) system was selected based on our expert domain knowledge.
As we finished the technical concept development, the computer simulation results were incorporated in the preliminary CAD. Further work concerned engineering development and CAD detailing.
In the engineering development of the vacuum cleaner, special attention was paid to deliver the explosion-proof design. Therefore all the equipment modules (both external and internal) were developed in compliance with the ATEX requirements (explosion-proof electrical circuits, exclusion of friction-induced and static charge sparks). Part of the solution was to cast a conductive antistatic polymer coating to the unit’s metallic surfaces. Sleeve filters also ensured antistatic protection (conductive threads woven into the fiber, grounded to the body through a conductive mount). Additionally, all electric circuits and control electronics ( a custom PLC controller) were designed in conformity with the ATEX.
Special attention was paid to the strength of the filter’s body. We had to be 100% sure the unit will survive the burst or explosion inside the hull. Therefore we ran additional FEA method analysis to ensure its integrity under explosion loads.
Additionally, we have designed a platform with a ladder at the vacuum cleaner’s upper zone to aid maintenance/repair convenience. Another developed feature was the top cover opening, aiding maintenance technicians in replacing filters without using heavy lifting equipment.
Having finished the design, EnCata mechanical and electrical engineers produced documentation and drawings for in-house unit production.
EnCata’s engineers designed and produced a vacuum dust cleaner developed in full compliance with the ATEX Ex-proof guidelines. The project was completed within a very short time - 3 months - from start to finish.
were produced and commissioned
of dust processed by the filter
vacuum is created by the filter’s turbine